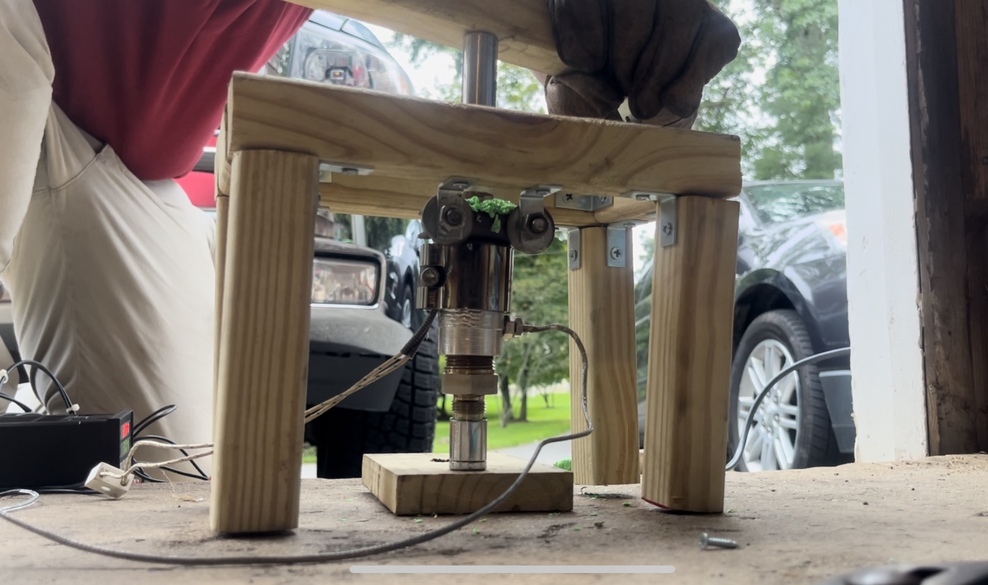
Today was a pretty big day. Although I only started building this prototype about a week ago, this idea is a long time in the making. Over this past winter, I tried something similar and achieved nothing but burnt plastic and some softened plastic that stuck together and was extremely brittle. That was the crude prototype, this is the slightly-less-crude prototype. Not only was I able to melt and plasticize plastic today, but I was also able to inject it into a mold of sorts.
Yesterday I mentioned that I had an idea for a low cost nozzle to be connected to the end of the barrel. That Idea was to use a flared reducer and tap the barrel to accept it. The round end which normally creates a mate to another piece of pipe works perfect as a sort of seal at the end of a nozzle.
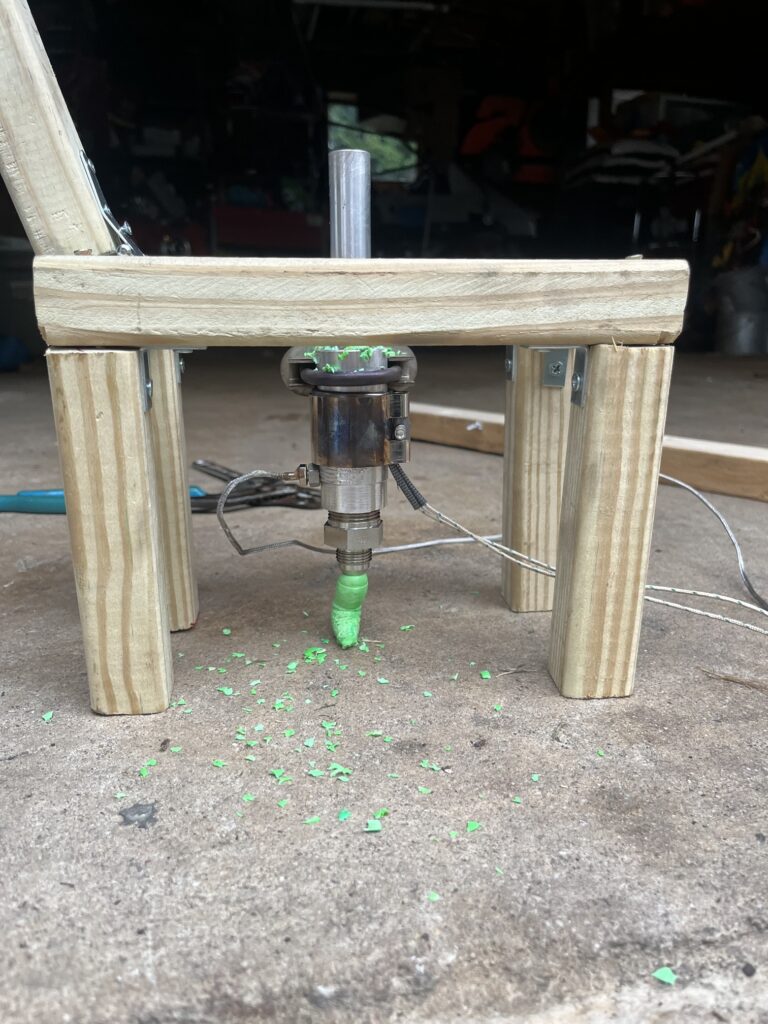
I am happy to announce that keeping with the idea of sustainability, I used recycled shreds of shampoo bottles for this first test! Surprisingly, the smell was quite pleasant, even at 230°F! One of the first things that I noticed was some foaming of the plastic. This is likely due to the shreds trapping air and I will have a solution for this soon.
Once I got plastic to start flowing through the nozzle, I got excited and wanted to try molding something. I still haven’t created any actual molds for this machine yet, but I got the bright idea to use a standard hex socket as a mold. While the socket doesn’t create a perfect seal against the nozzle, it would be a good test to see if the plastic could flow enough to form a shape inside of the mold.
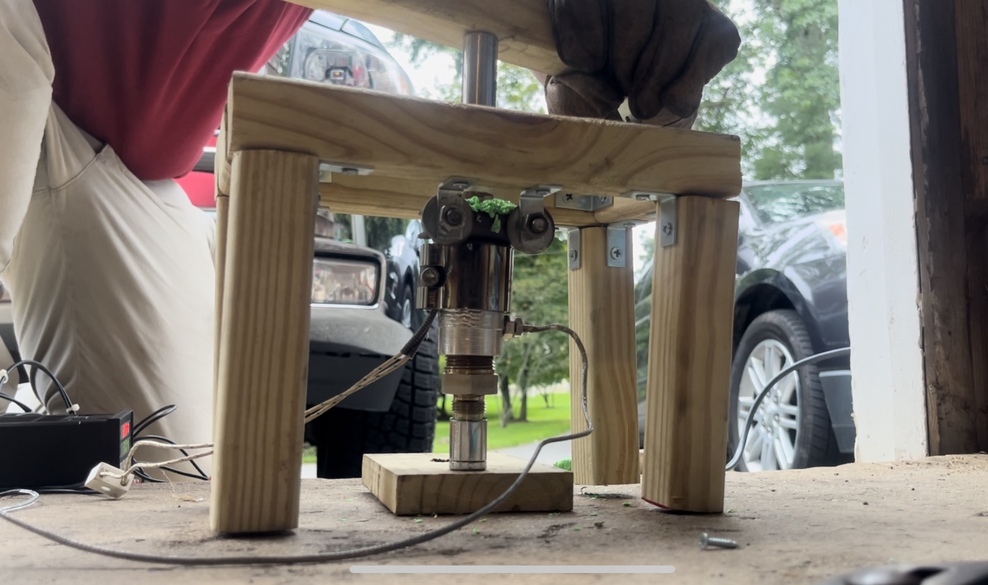
I was honestly quite surprised with the result. The plastic took to the shape better than I thought it would and I may begin using this test to compare results when I start focusing on making the machine function better.
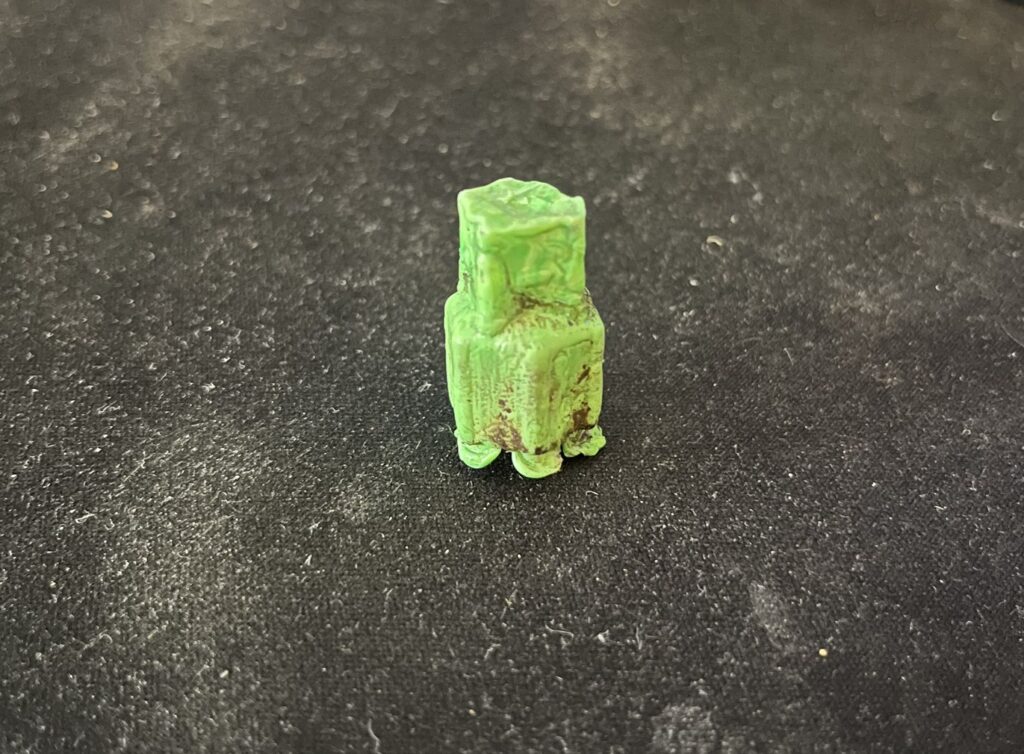
That brown stuff is rust by the way not burnt plastic. The part is strong too, not brittle owing to my belief that the machine was able to begin plasticizing the polymer. Next, I am going to rebuild the test stand using the new tools I picked up yesterday to make the process of heating and injecting safer and more reliable as the wooden test stand clearly leaves alot to be desired.
Before I go, I thought I’d give you a bit of a teaser and show off the dimensional accuracy possible, even when using this crude of a version of this machine. You tell me, can you guess what size socket was used as a mold when this was injected? ☺
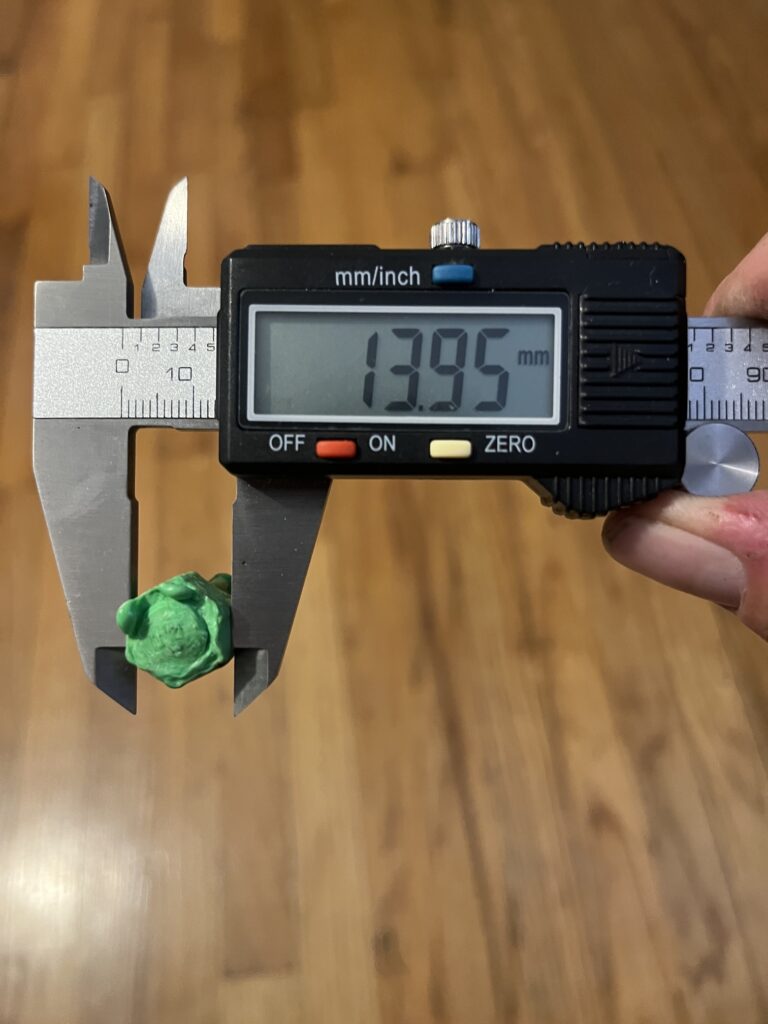