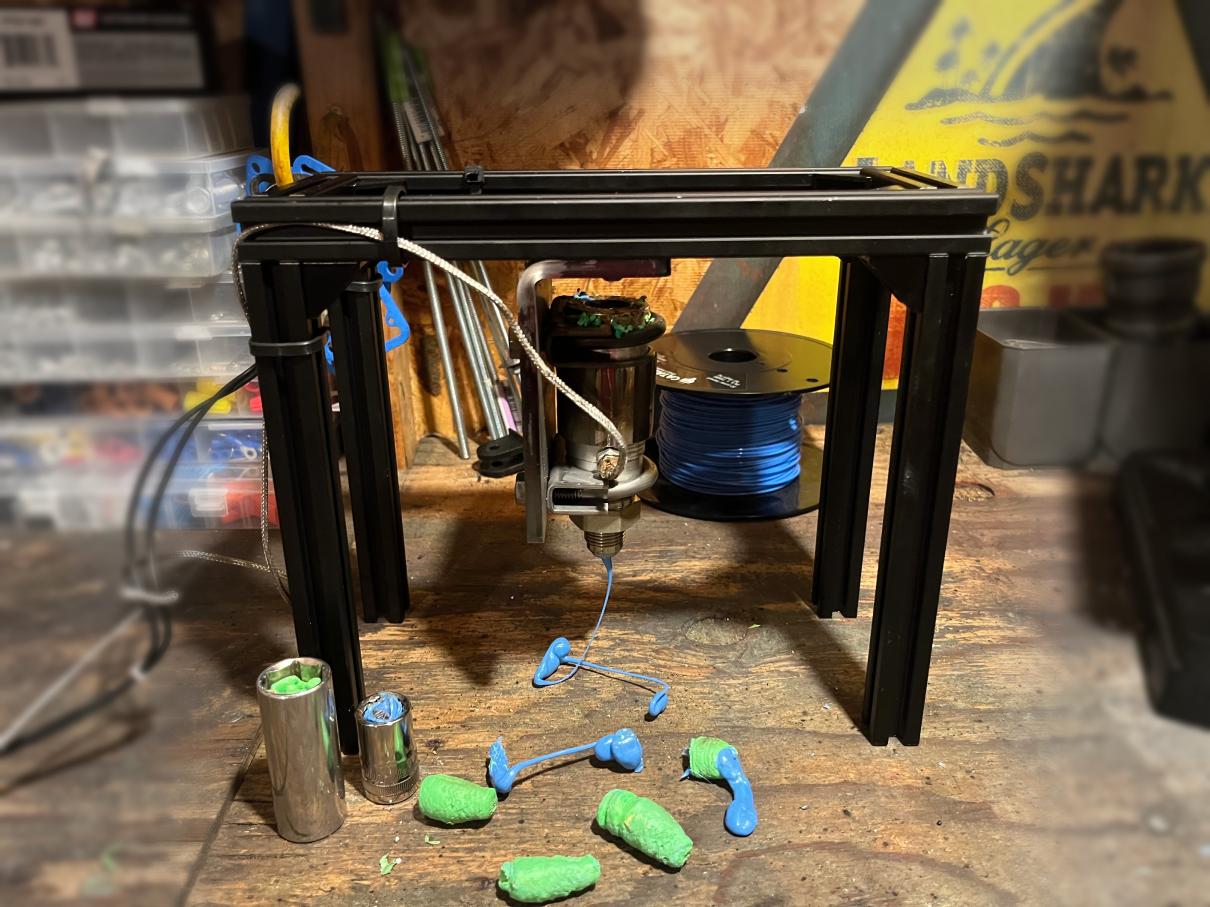
Hi all, I was able to finally attach the new barrel mount to the frame today and get some injection cycles through it. The new assembly is much sturdier and makes pushing plastic through the barrel a lot easier. I was also able to play around with different injection temperatures to see what effects it had on the machine.
As was the same in my previous posts, I used recycled shampoo bottles as plastic to test the machine. You might be able to see that the green plastic that comes out of the nozzle is quite puffy. I believe this is due to the leftover detergents and pigments in the plastic vaporizing and puffing the plastic up into a semi-foamy material.
While messing around, I decided to put some old 3D printer filament in the machine and see what effect that had. The result was much better than the plastic I used before! While this isn’t recycled plastic, it is PLA which is a more environmentally friendly plastic than others typically used in the plastics manufacturing industry.
I attempted to do more injections using sockets as molds but unfortunately, I forgot to put mold release on them and the plastic is stuck down in them. Next time, I will prepare the “molds” better so I can test the dimensional accuracy.
Either way, I think I have a good platform to begin iterating and optimizing the machine. I already have lots of ideas on what can be improved on. For one, dealing with the hot plunger and barrel is becoming a serious hinderance so I will have to find a way around that. As I mentioned before, I want to make some soft tooling so that I can start injecting usable parts rather than the inside of a socket.
For now, I’ll be going back to the drawing board to think up some of these improvements and get them manufactured. I’m starting to get to the point where I need to do some calculations and testing to begin optimizing the machine and I’m excited to share that process with you as I do it!
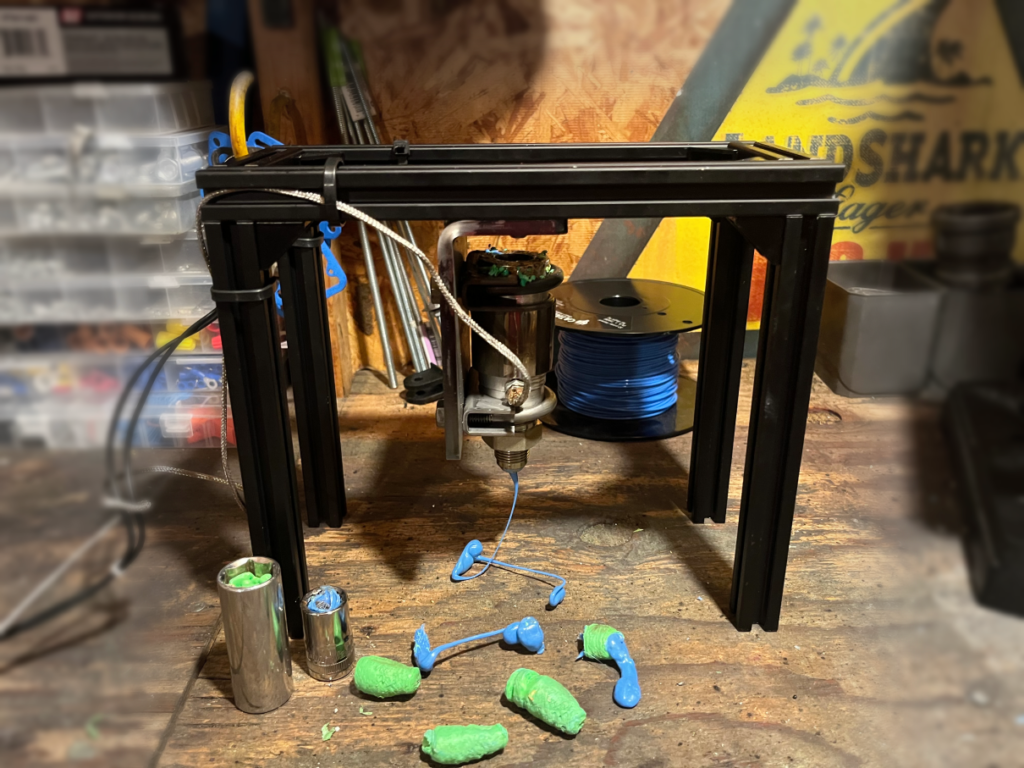